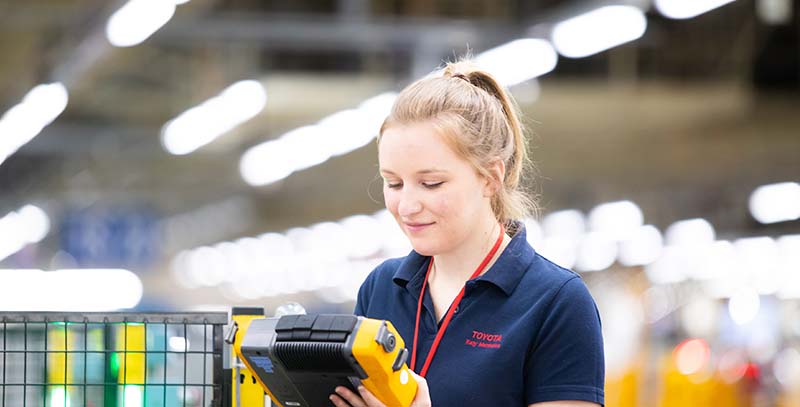
Engineering
Engineering at Toyota isn’t about nuts and bolts. It’s much more about having imagination plus the dedication to keep developing the best processes and products.
We encourage our engineers to look at things from every angle to find better ways of working. That’s always been the Toyota Way – as our founder Sakichi Toyoda put it: “Inspiration comes from many places. We need to have our eyes, our minds and our hearts open to things we interact with every day, so open your window to the world.” You can see that commitment reflected in cars like the Corolla. It’s what makes Toyota an outstanding place to work for inquisitive and ambitious engineers.
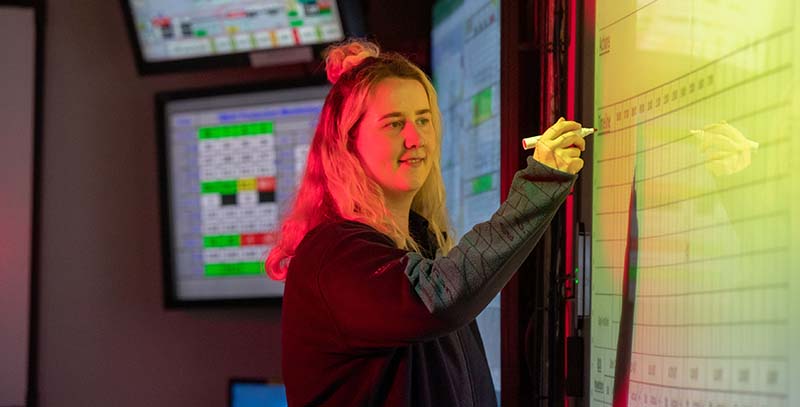
Production Control (Supply Chain)
Everything starts and stops with Production Control and our Supply Chain. Join us here as we control, plan and continually kaizen our vehicle and parts flow and you'll be at the centre of our manufacturing operation bringing the world-famous Toyota Production System* (TPS) to life.
You will have the opportunity to learn about concepts like just-in-time (JIT) first-hand from the company that pioneered them whilst empowering you to incorporate your innovative ideas and solutions in an ever changing digital environment.
*TPS is a lean manufacturing system designed to eliminate waste, reduce costs and keep lead times down - where Toyota has led the way, other manufacturers have followed.
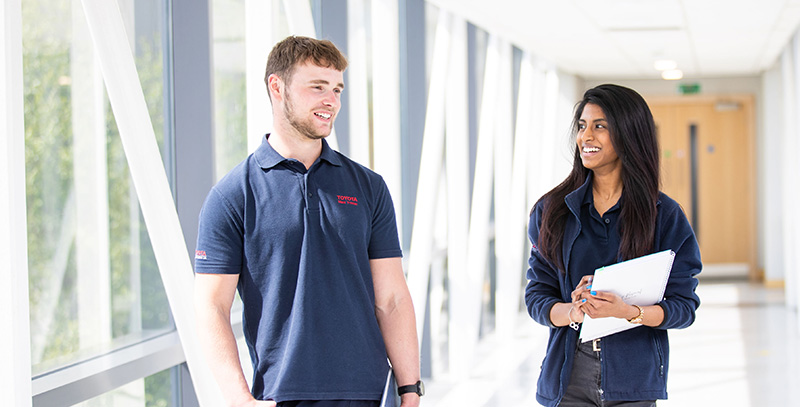
Human Resources
Our approach to people management is different.
One of Toyota's Guiding Principles is to foster a respectful, reflective culture where individual creativity and teamwork can flourish. That makes HR a visible, valuable part of our operation. To keep our products progressing and our processes evolving, it’s essential to develop our people. Our HR specialists are influential experts, and most employment issues are their business. To succeed in HR, you’ll need to be a team player yourself – as comfortable and confident on the shop floor as you are with your senior managers.
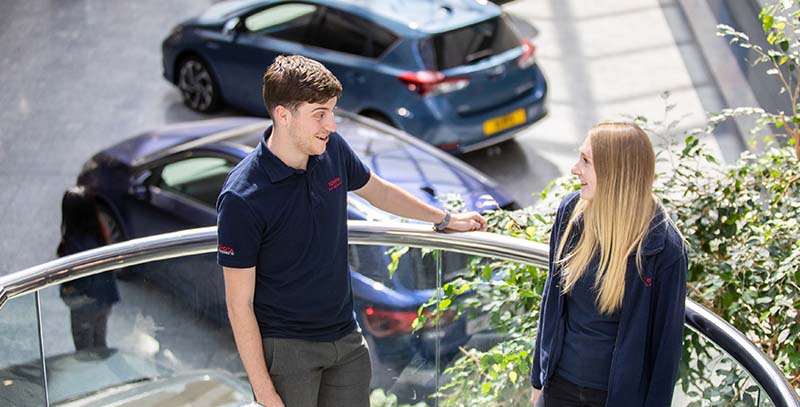
Finance & Purchasing
Finance isn’t a back office function at Toyota.
You’ll soon see that a key part of your role is to go and see things for yourself and adopt a dynamic and practical learning method. You’ll spend time on the shop floor and understanding the way we work from a manufacturing perspective. A key part of our role is to develop breakthrough initiatives to manage costs per vehicle by working closely with other departments. Whether you are in cost management, general ledger, accounts payable and received, purchasing, or investment, you'll tackle real commercial projects and discover how finance can add real value to the production process.